Share
Pin
Tweet
Send
Share
Send

Will need
To make it, you need time, considerable effort, utmost accuracy and the following materials:

- stainless steel bolt M20 × 70;
- thumb wheel;
- tools for applying numbers to the wheels;
- steel balls;
- spring steel wire (0.3 and 0.8 mm).
From the equipment we can not do without:
- turning, drilling and milling machine;
- vice of metalwork;
- pliers;
- hacksaws for metal;
- grinder;
- scissors for metal and paper cutting;
- mandrels for winding springs and snap ring.
Manufacturing technology
The work consists of three stages: manufacturing of parts and assemblies, assembly and installation of a code combination of numbers.
Production of parts and assemblies
Side locks
On a lathe, we divide the bolt head into two halves, and we drill the rod to the depth of the thread profile.


We clamp one part of the rod in a vise and saw it with a metal saw into two longitudinal halves.


On one of the hexagonal plates with the help of a template and a marker, apply the outline of the side pad of the lock.

We grind glued hexagons on the grinder along the drawn contour of the side lining of the lock and drill holes at the ends.


We insert into the holes the "legs" of the round patterns used only to display the contour of the side plates of the lock on the grinder.

On the drilling machine with a drill and an end mill in the side plates we form the finish profile of the holes. Around the large hole evenly in a circle we carry out an end mill of 9 recesses.

We use a soft circle to polish all the surfaces of the side plates of the lock.


Pins
Of the 4 half-cylinders, using a special clamp, we sharpen a round bar on the lathe to the middle of the workpiece.




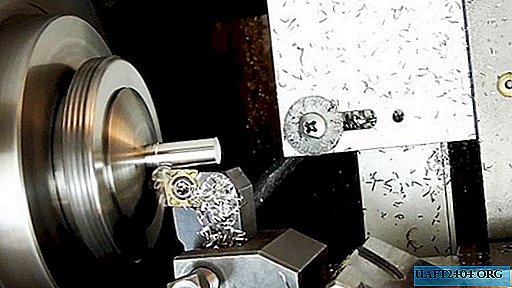
The first pin is for wheels on the side of the mount. On the one hand, it has a seat for a hole, on the other - an annular groove for a retaining ring and a blind hole.

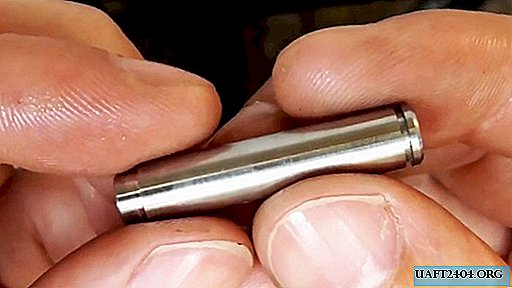
With a milling cutter, we perform a longitudinal groove in it for the entire length of the blind hole.




The second pin on the fastening side looks like a solid round rod with a seat for a hole in the side plate of the lock and blind longitudinal drilling.






The third pin key on the moving side also extends under the solid cylinder. Then, on one side, it is clamped into the cartridge with a gasket to offset the axis of the roller to the side from the axis of rotation of the cartridge. As a result, when processing with a cutter, a round tenon of a smaller diameter is formed, the center of which does not coincide with the center of the pin.



Then, by milling, we form two shelves on both sides of the offset tenon. As a result, a rod with two faces connected by circular arcs comes out.

With the same cutter, we reduce the cross-section of the rod from the larger side by symmetrical processing.


The end mill performs 5 rectangular and equal grooves. As a result, 5 equal protrusions are also formed.
Files, files and emery paper give the core with all the protrusions the desired shape and round off the edges and ribs. At the end, this and all other rods are polished with a soft circle.



Insert the rod into place in the side pad of the lock.
The fourth pin, which acts as the upper shaft on the moving side, is pierced to the size of the hole in the side plate of the lock and, on the one hand, is filed in a hemisphere with a file and a soft circle. We also insert it in its place.



Welding, grinding, polishing
We weld all the pins on the back to the side plates of the lock.
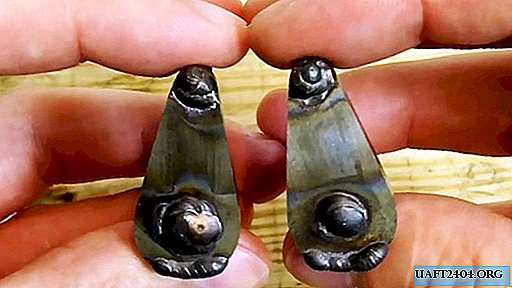
We grind and polish the welds on the grinder, round the edges with a file, finish with sandpaper and polish with a soft circle.

With a set of files, we form a groove at the end of the pin with a longitudinal slot. We try on the entry of the movable pins into the holes of the motionless ones.



Brass wheels with numbers
We make 4 brass wheels with numbers. We cut their workpieces after grooving to the size on a lathe, first drilling a through hole in the center, and expanding it, on the one hand, to a certain depth.





The fifth wheel differs from the others by the presence of a central groove on both sides, one of which is deeper than the other.
Columns of numbers for printing onto wheel generators are printed on mirror coated paper in silicone.
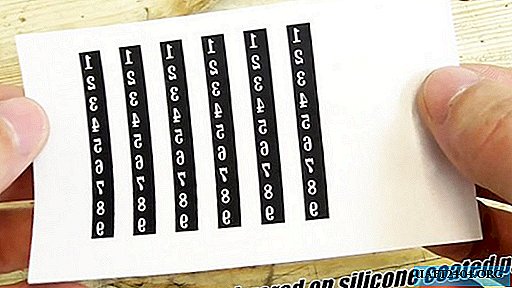
We cut the vertical strips of numbers with scissors and paste them on the generators of the wheels.

We translate the numbers onto the surface of the forming wheels, running them around the sole of the hot iron. As a result, the paper separates, and a layer of silicone with numbers sticks to the ring.


For protection, all surfaces of the wheels, except those forming with numbers, are covered with nail varnish.

We string the wheels onto the wire, put it at the bottom of the inclined cell and pour iron chloride solution for etching for 45 minutes, which makes the wheels attractive, and the numbers are contrasting.


Next, we string the wheels onto a special mandrel, tighten with a nut and clamp in the lathe chuck. Next, we process the wheel block with sandpaper and polish with a pile cloth.
We clamp the wheels in a special holder and use a milling machine to make a semicircular groove with a mill and exit to a large hole.
At the ends of the wheels we carry out 9 recesses evenly in a circle.


We fix the wheels one by one on the mandrel and clamp in the lathe chuck. We bring the adjusted knurling to the wheel, lubricate them with oil and turn on the machine. A circular notch is rolled on a wheel at the end of a narrow strip.


The cutter removes the burrs from the end of the notch.
We drill with a drill 0.8 mm blind holes in the ends of the wheels with a notch opposite a semicircular groove.

Again, we put the wheels in turn onto the mandrel and apply black paint to the digital recesses, removing excess with a flat surface, pressing it against a rotating wheel, and then with a soft cloth.



Additional details, assembly and coding
Using a special mandrel for winding springs, mounted on a lathe, we produce 5 such springs from 0.3 mm spring steel wire.


To hold the wire on the mandrel when winding the springs, we use pliers, and for cutting the ends - scissors for metal.
To assemble wheels with numbers, in addition to springs, we need 5 steel balls per 2 mm.

We insert into the blind holes in the wheels along the spring and cover with a ball from above.


Then all 5 wheels with springs and balls are strung on the upper shaft.
From a spring steel wire of 0.8 mm on a simple mandrel, clamped in a vice, pliers and wire cutters, we make a stop-lock for squeezing and holding the wheels with numbers on the shaft.

We tweezers insert one end of the stopper into the groove on the end of the rod, press the stopper in the middle, then the second edge reliably covers and holds everything under it.



It remains to insert the second sidewall of the code lock with the rods in their place and the device is ready for operation. But while the lock is locked, because a random combination of numbers is set. Code dialing is determined by the location of the locking elements on the wheels and is exclusive for each lock.


Share
Pin
Tweet
Send
Share
Send